Richmond Elevator B44-M90 Hydraulic Controller
Safety Order
Safety Order: Richmond Elevator B44-M90 Hydraulic Controller
September 6, 2023
Reference Number:
SO-ED 2023-01
This safety order is issued pursuant to section 31 of the Safety Standards Act. A person affected by this safety order may appeal this order in writing to the Safety Standards Appeal Board within 30 days. The appeal process is set out on the Safety Standards Appeal Board's website at www.gov.bc.ca/safetystandardsappealboard.
Failure to comply with a safety order is an offence under section 72 of the Safety Standards Act.
Part 1: Details of Regulated Product
The safety order is being issued in relation to a specific regulated product – specifically Richmond Elevator hydraulic elevator controllers installed to the CSA B44-M90 code edition.
The following issue was identified as the main causal factor during an incident investigation performed by Richmond Elevator and Technical Safety BC:
In the scenario where a leveling switch fails, the elevator will continue to operate but will fail to stop substantially level with the adjacent landing, creating a trip hazard to passengers loading or unloading from the elevator.
Clause 3.12.9(c)(ii) of CSA B44-M90 requires the occurrence of a single ground or the failure of any levelling switch shall not permit the car to move beyond the levelling or truck zone and clause 3.12.9(d) requires the car shall not be permitted to restart when a single ground or failure occurs.
The following models of controllers are affected:
Richmond Elevator hydraulic controllers installed between October 1, 1991 and December 31, 1994.
Non-compliances for units identified with Richmond Elevator hydraulic controllers installed between October 1, 1991 and December 31, 1995, will be automatically assigned to the associated operating permit(s).
Part 2: Requirement(s) Of This Safety Order
Verification of non-compliance and obtaining replacement parts:
Send the following information to Vladimir.Aniks@richmond-elevator.com, including the site address and (Technical Safety BC) unit identification number:
- Send the elevator to the top floor.
- Take a photograph of the Input/Output list on the front of the PLC that contains the inputs from the leveling switches (DL and UL) (see example 1).
Where required, Richmond Elevator will provide refurbished backplates with updated software for identified elevators and deliver the part to the licensed contractor performing this repair. The removed original backplates are to be returned to Richmond Elevator at the following address:
c/o Vladimir Aniks
12091 No 5 Rd, Richmond, BC V7A 4E9.
If Richmond Elevator confirms that a replacement back plate is not required, skip to Part 3: Reporting Requirements.
Repair Process
Once the replacement parts have been received, the following process is required to complete the repair:
- Place elevator on independent service operation at the lobby floor.
- Remove electrical power to the elevator at the machine room disconnect, following lockout-tagout procedures.
- Unplug the power supply to the PLC.
- Unplug all I/O cards.
- Remove the existing back plate – removing 4 connecting screws.
- Install the replacement back plate provided by Richmond Elevator – attaching with 4 screws.
- Re-plug the power supply to the PLC and re-plug the I/O cards.
- Restore electrical power at machine room disconnect to the elevator and restore elevator to normal operation to perform required testing.
Test Procedures
Test 1: UL Switch Failure – determine that a failure of the leveling switch UL does not permit the car to move beyond the leveling zone.
- While the elevator is at the floor, install a temporary a jumper from terminal 11 to terminal UL.
- Observe that the elevator starts moving in UP direction in slow speed.
- Observe that the elevator stops when it reaches the leveling switch DL.
- After 5 sec. observe two outputs on output card (1FL and TFL) start flashing.
- Remove the jumper.
- Observe that the elevator will not accept any hall or car calls.
- A manual reset is required to restore operation.
Test 2: DL Switch Failure - determine that a failure of the leveling switch DL does not permit the car to move beyond the leveling zone.
- While the elevator is at the floor, install a temporary a jumper from terminal 11 to terminal DL.
- Observe that the elevator starts moving in DOWN direction in slow speed.
- Observe that the elevator stops when it reaches the leveling switch UL.
- After 5 sec. observe two outputs on output card (1FL and TFL) start flashing.
- Remove the jumper.
- Observe that the elevator will not accept any hall or car calls.
- A manual reset is required to restore operation.
Test 3: Backplate I/O Verification - determine that the replacement backplate is functioning correctly.
- While the elevator is at the floor, place a jumper from terminal 11 to all car call terminals (1F, 2F, ..., TF).
- Observe that the outputs in the output card are activated (e.g., 1FL, 2FL, ..., TFL) and that the elevator responds to each car call appropriately.
- While the elevator is at the floor, place a jumper from terminal 11 to all hall call terminals (1U, 2U, 2D, ..., TD).
- Observe that the outputs in the output card are activated (e.g., 1UL, 2UL, 2DL, 3DL, ..., TDL) and that the elevator responds to each hall call appropriately.
Part 3: Reporting Requirements
Once the repair process and associated testing has been completed, the licensed elevating device contractor completing the repairs shall submit a report in the form of the non-compliance completion declaration form (FRM-1073). All repairs, testing and associated non-compliance completion declarations shall be completed by December 31, 2024.
Where Richmond Elevator confirms the existing backplate is compliant through the verification stage, report this by submitting a non-compliance completion declaration form (FRM-1073) with a copy of the confirmation from Richmond Elevator.
Where the Richmond Elevator hydraulic controller has been replaced with a model not referenced in this Safety Order, report this by submitting a non-compliance completion declaration form (FRM-1073) with a note in the “Date Completed” section stating “Controller replaced. Safety Order is not applicable.”
Part 4: Details of Ordering Safety Manager or Safety Officer – Please Read the Following Page
I certify that I am authorized to issue this safety order in accordance with section 15 (d) of the Safety Standards Act or that I have been delegated this power under section 15 (g) of the Safety Standards Act.
Nav Chahal
Provincial Safety Manager - Elevating Devices
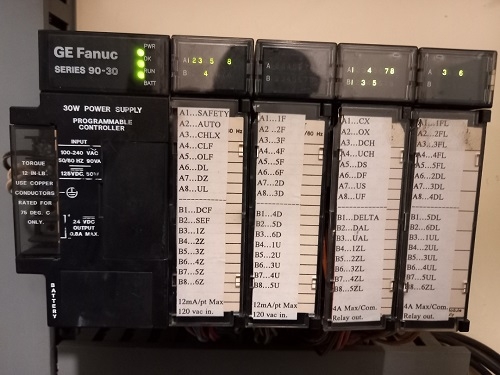
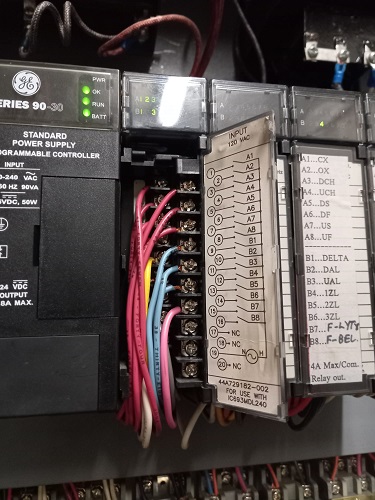
Safety Standards Act
Safety Orders
31
(1) To prevent, avoid or reduce risk of personal injury or damage to property, a provincial safety manager may, in writing, issue a safety order.
(2) A safety order may be issued to any person in relation to any of the following:
- regulated work or regulated products generally;
- a specific class of regulated product or regulated work;
- a specific regulated product or regulated work.
(3) For certainty, a safety order issued under this section may apply to
- regulated work that meets the requirements under this Act,
- regulated work that previously met the requirements under this Act or a former Act but does not meet the current requirements under this Act,
- regulated products that meet the requirements under this Act, or
- regulated products that previously met the requirements under this Act or a former Act but do not meet the current requirements under this Act, including a regulated product that bears a certification mark.
(4) A safety order may specify any requirement that is intended to prevent, avoid or reduce the risk of personal injury or damage to property and may include any of the following orders:
- that an existing regulated work or regulated product must be made safe in compliance with the safety order;
- that a regulated product must be
(i) disconnected from a power source,
(ii) uninstalled, or
(iii) modified before continued use; - that a regulated product must be operated, installed, manufactured or disposed of only as specified or that a regulated product must not be moved;
- that current or future regulated work or a regulated product must conform to the terms or conditions of the order;
- that a person take or refrain from taking any action that a safety manager considers necessary to prevent, avoid or reduce a risk of personal injury to persons or damage to property;
- that the manufacturer make reasonable efforts to recall the regulated product.
(5) The provincial safety manager must give written notice of the safety order to the following persons:
- the manufacturer of the regulated product;
- an owner of the regulated product if the identity of the owner is known to the provincial safety manager;
- the person in charge of the regulated work.
(6) The notice must state the reasons for the decision and that the person has the right to appeal the decision to the appeal board.
(7) Despite section 54, a safety order may not be stayed during an appeal.
References:
Safety Standards Act
CSA B44-M90
Non-Compliance Completion Form 1073