Risks in Focus
Annual State of Safety 2024
The Hidden Costs in Cutting Corners:
Three Common Misconceptions in Technical Safety
Extending equipment life or maximizing production schedules might appear as smart cost-saving strategies, but we’ve seen multiple incidents that prove these practices come with a hidden price. In the long run, these common misconceptions lead to higher financial costs, greater safety risks, and ultimately, worse business outcomes.
Misconception #1: If It’s Not Broken, Don’t Fix It
Waiting until equipment is no longer functioning properly may seem like a good cost-saving mindset, but when it comes to technical equipment, waiting for equipment to fail can easily become dangerous.
Over the years, we've seen firsthand how poorly maintained aging equipment leads to preventable incidents. For instance, in a food processing facility, an autopurger was in use well past its manufacturer-recommended lifespan. It malfunctioned and released ammonia instead of air into a room of workers, with two people suffering first and second-degree burns.
A functional autopurger removes air from a refrigeration system to keep ammonia running smoothly and safely. However, in this incident, investigators found the autopurger had deteriorated into a state of disrepair, including missing knobs and internal fouling. Multiple ammonia releases had also occurred prior to the incident, but none were reported. Minor repairs and procedural checks were done following these incidents, and the autopurger was put back into operation. Additionally, while a third-party contractor had recommended replacing the autopurger, this advice was not actioned by management.
The incident resulted in the facility being closed while they replaced equipment and complied with investigations. While this incident was serious, the facility was fortunate not to have more devastating consequences as a result of the malfunction, as ammonia release is listed on our Top 5 Safety Risks for 2024. The tragic incidents in Fernie, BC and Kamloops, BC, remind us that ammonia gas is toxic and can be deadly.
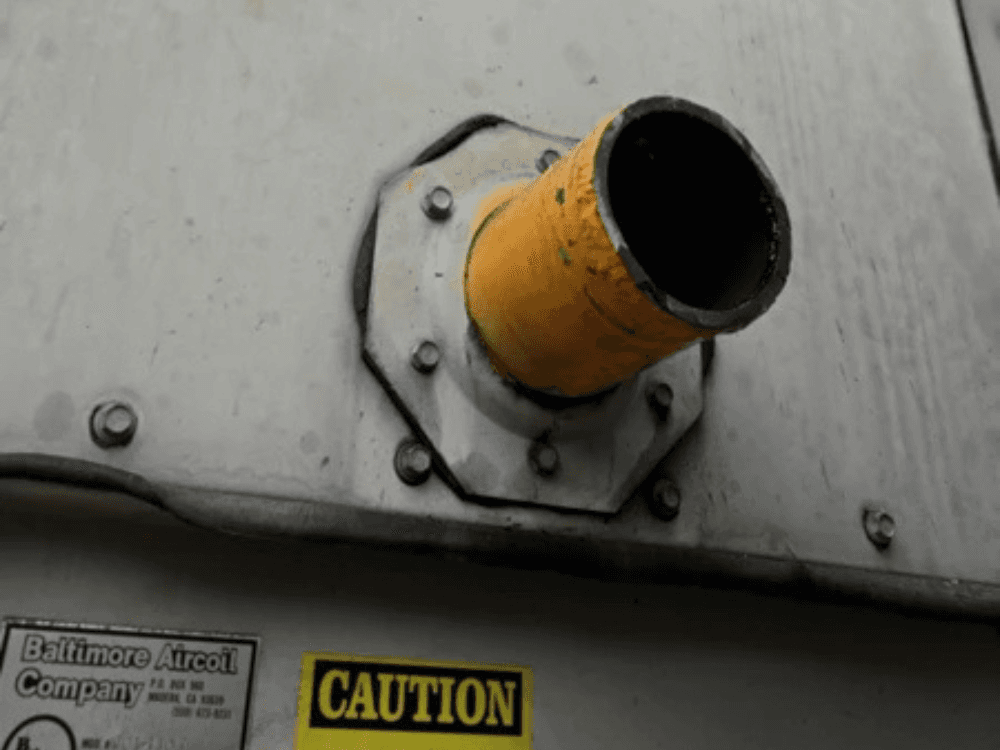
Misconception #2: The Show Must Go On
Continuing production at all costs might make sense in a theatre, but when it comes to regulated equipment, disregarding potential dangers may lead to catastrophic consequences. Incidents have occurred when warning signs of failing equipment were ignored until it was too late.
For example, at a pellet mill, an explosion occurred in the combustion chamber which loosened combustible dust and caused a secondary explosion in the dust collection system of the plant. Workers were injured, and others were nearly injured. There was significant damage to the plant.
Before the explosion, the burner was repeatedly noted to be functioning improperly and was restarted three times in a span of 18 hours to keep production running. The incident occurred after the final restart.
Investigation into the incident found that set points for gas pressure and airflow in the system were not within specification, causing significant combustion problems.
By choosing to restart the system without addressing the underlying issues or calling in a gas technician to inspect the burner, the decision to "keep the show going" ultimately led to a preventable incident — resulting in costly downtime, significant safety risks, and unnecessary harm.
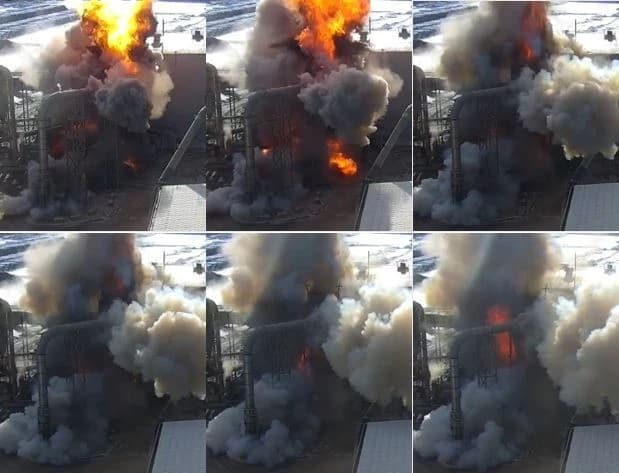
Misconception #3: A Penny Saved is a Penny Earned
Stretching resources might be valued as maximizing business efficiency but the consequences of inadequate staffing and resources can be far greater than any cost savings.
At an adventure zipline course, a rider careened into a rolling metal staircase at 60 - 80 km/h, resulting in a life-threatening leg injury, and damage to the staircase.
The rolling metal staircase, which was used for riders to disembark, had to be repositioned on the right- or left-hand sides of the platform before the next rider was given the “fly” signal. At the time of the incident, the staircase was not put back into position before the next rider was signaled to go.
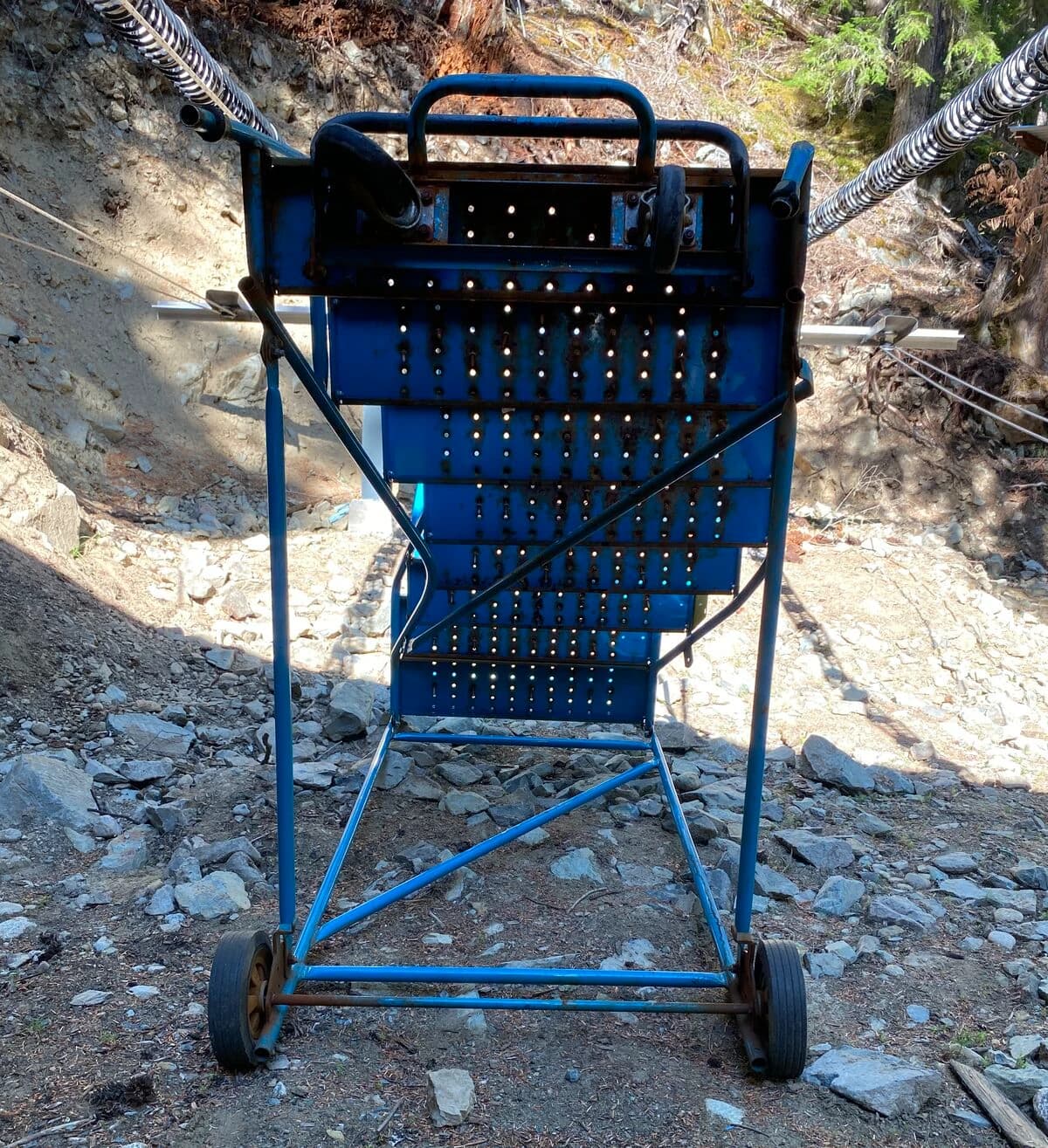
At first glance, this may seem like a simple case of oversight by the guide. However, investigators found that stress and mental fatigue due to lack of staffing may have played a role in the incident.
On the day of the incident, the guide was on their third and final tour — the maximum allowed in a day. In each tour, the minimum guide-to-patron ratio was used. With no breaks between tours other than washroom visits, the guide was stretched thin. They were the only guide on the lower platform, juggling multiple tasks: answering guest questions, unhooking and dismounting riders, checking braking systems, and making sure that previous riders stayed in their designated zones to avoid collision with other guests. The lean staffing level likely placed stress on their ability to safely perform their duties.
The guiding procedure included a “six-point check” and radio protocol, but nothing in the training addressed the use of the rolling staircase. When the platform changed and required the use of a rolling staircase, no risk assessment was conducted to understand the new risks or how to minimize them.
After the incident, the zipline was shut down for an extended period, drawing media attention. This incident possibly further influenced public distrust of the ziplines industry, especially since it wasn’t the first time an incident of this nature occurred.
The incident could have been avoided by lowering the risk of human error through increased staffing, adequate breaks, and updating training that covered all equipment and potential hazards.
Informed Decisions, Safer Outcomes
The difference between preventable incidents and those that are avoided relies on proactive decision making. It's the responsibility of equipment owners to decommission or replace machinery before it reaches an unsafe state. Taking the time to check malfunctioning equipment, even if it means temporarily stopping production, can prevent worse consequences in the future. Finally, understanding the human factors in safety outcomes is essential for improving both safety and operational efficiency.
Many British Columbians play a vital role in maintaining the integrity of the safety system, and it's essential that those who own, operate, oversee, hire, or perform regulated work on equipment fully understand and meet their responsibilities. To support this, we are working to provide clearer guidance on regulation, codes and standards, helping decision makers better understand their role. Specifically, in 2024, we implemented a process where client declarations for decal permits can be accepted in the boilers, pressure vessels, and refrigeration technology. Additionally, we analyzed gaps that may lead to safety hazards for in-service elevators: cultural understanding of roles and accountability; regulatory inspections or declarations; and the allocation of resources. We will soon begin to pilot short-term solutions and develop longer term strategies to support shared accountability in the safety system.
You Might Be Interested In
Top 5 Safety Risks
From carbon monoxide to electrical shock and fire, learn about the Top 5 Safety Risks we identified for 2024.
Learn MoreSafety Engagement
We provide technical training and education to support our partners. We also work to influence people in the safety system to make safety-minded decisions.
Learn MoreData and Trends
Find key statistics on permits, incidents, injuries, assessments, and more.
Learn More