Class A Syllabus
Pressure Welder Certification
Overview
Every applicant for a Class A Pressure Welder certificate of qualification must successfully pass a welding examination administered in the form of a performance qualification test to meet the requirements of Section 41(2)(b) of the Power Engineers, Boiler, Pressure Vessel, and Refrigeration Safety Regulation. This syllabus details the requirements and standards for the performance qualification test.
Eligibility to Apply for Examination
An applicant for a Class A Pressure Welder certificate of qualification must hold one of the following:
- a BC welder certificate issued by Skilled Trades BC and endorsed with a Red Seal credential;
- a BC welder level A or B certificate issued by Skilled Trades BC;
- a welder trade qualification, endorsed with or without a Red Seal credential, by an apprenticeship authority in another jurisdiction of Canada.
Application to Undertake Examination
A candidate for examination shall submit a completed application to Technical Safety BC, proof that they meet the eligibility requirements for a Class A Pressure Welder certificate of qualification examination and pay the specified fee.
Examination Administration
After acceptance of the application by Technical Safety BC, the Class A Pressure Welder certificate of qualification examination shall be carried out at a host location accepted by Technical Safety BC and shall be conducted and administered by a Technical Safety BC safety officer.
Candidates must show original and unexpired government issued photo identification to the safety officer prior to starting the examination.
Note: A list of the host locations is posted on the Technical Safety BC website. All equipment used for the examination must be of known calibration and a bend test jig must be available, in accordance with ASME Section IX. All equipment must be acceptable to the safety officer.
Class A Pressure Welder Certificate Examination
The following procedure outlines the manner in which the Class A Pressure Welder certificate of qualification examination will be administered by a safety officer.
Test Coupon
The test coupon will be a 6-inch diameter schedule 80 carbon steel (P1 material) seamless pipe and prepared with a 32-degree bevel to a feather edge.
Test Positions
1/4 of the coupon circumference will be welded in the 2G (horizontal) position and the remaining portion in the 5G (fixed vertical) position.
Electrodes
Candidates have two options for the tacking and root pass of the exam. One option must be selected and confirmed with the safety officer prior to starting the examination:
- option 1: SMAW process using electrode E-6010, 1/8” diameter.
- option 2: GTAW process using an SFA 5.12 classified tungsten electrode and ER70S-2 filler metal, 3/32” or 1/8” diameter. 100% Argon and no backing gas shall be used for this option.
The hot pass and fill passes shall be completed using the SMAW process and electrode E-7018, 3/32” and 1/8” diameter. The 5G cap pass shall be completed using 3/32” or 1/8” diameter electrode. The 2G cap pass shall be completed using 1/8” diameter electrode.
Examination Time
Candidates will have 3.5 hours to prepare, tack, and weld the test coupons and 1 hour to prepare the bend specimens.
The examination may be terminated by the safety officer at any stage of the evaluation if the candidate fails to meet the acceptance criteria or is unable to complete the examination within the specified timeframe.
Preparation and Tacking
When preparing test coupons for tacking, the size of the root face (land) and the width of the root gap (spacing) shall be at the candidate’s discretion. Prior to tacking, mill scale, coatings, and burrs should be removed. Four tack welds, one centered at each quarter of the circumference of the pipe, are to be made using the SMAW process with an E-6010 electrode or the GTAW process using an ER70S-2 filler metal and should be approximately ½” to ¾” in length before feathering. All tack welds are to be considered part of the weld and should be of acceptable quality with no cracks, complete fusion, and joint penetration.
Welding
After the candidate completes tacking of the coupon, they will present it to the safety officer for evaluation. The safety officer will evaluate the quality of the tack welds and then mark the portion of the coupon that is to be welded in the 2G position with the remainder to be used for welding in the 5G position. Candidates may feather the tacks after the safety officer’s evaluation.
After the safety officer’s evaluation, the coupon is positioned for welding in the 2G position. The candidate will then weld the 2G root pass using the SMAW process with an E-6010 electrode or the GTAW process using an ER70S-2 filler metal with the pipe axis in the vertical plane. When the candidate completes the 2G root pass the weld shall be visually inspected by the safety officer. The root pass shall be of uniform width and the penetration shall be at least flush with a maximum reinforcement not exceeding 1/8”. It shall also be free of any undercut, grapes, lack of fusion, or porosity.
Providing the 2G root pass is acceptable, the coupon shall then be placed in the 5G position (pipe axis in the horizontal plane) with one end of the completed 2G root placed at the top (12:00). The safety officer will mark the position and height of the coupon. Once the coupon is positioned for welding, the marked coupon and positioner shall not be moved. The candidate will then weld the 5G portion of the root pass using the SMAW process with an E-6010 electrode with an upward progression or the GTAW process using an ER70S-2 filler metal with an upward progression. The coupon shall remain in the positioner and the weld shall be visually inspected by the safety officer upon completion of the 5G root pass. The root pass shall be of uniform width and the penetration shall be at least flush with a maximum reinforcement not exceeding 1/8”. It shall also be free of any undercut, grapes, lack of fusion, or porosity.
If the root pass is acceptable to the safety officer, the candidate shall complete the hot pass, fill, and cap passes of the 5G section using the SMAW process with an E-7018 electrode in an upward progression and using a single weave method for the cap. The coupon shall remain in the positioner and the weld shall be visually inspected by the safety officer upon completion of the 5G hot pass, fill, and cap passes. The cap shall be of uniform width, at least flush with a maximum reinforcement not exceeding 1/8”, and free of any undercut, grapes, lack of fusion, porosity, or arc strikes.
If the 5G hot pass, fill, and cap passes are acceptable to the safety officer, the coupon will then be repositioned (axis in vertical plane) to complete the 2G position hot pass, fill, and cap using an E-7018 electrode using a stringer bead method. The coupon shall remain in the positioner and the weld shall be visually inspected by the safety officer upon completion of the 2G hot pass, fill, and cap passes. The cap shall be of uniform width, at least flush with a maximum reinforcement not exceeding 1/8” and free of any undercut, grapes, lack of fusion, porosity, or arc strikes.
Repairs at any stage of the examination are not permitted. Repairs include any welding on the inside diameter of the coupon and any use of a grinder, file, or other tool that is not for the purposes of feathering, slag removal, cleaning of the coupon or weld passes, and bend specimen preparation.
Bend Testing Specimens
Four face bend and four root bend test specimens are required for this examination. Test specimens will be marked on the coupon by the safety officer as per the following sketch. The specimens shall be removed by the candidate manually using an oxyfuel torch, bandsaw, or grinder. Specimens must be no less than 6” in length,1.5” in width, and ground flush on both sides with edges de-burred. Candidates may radius the corners of the specimens to 1/8” maximum.
Excessive grinding that reduces the thickness of the specimens below the nominal thickness (on either side) shall result in failure of the examination.
Bend Specimen Locations
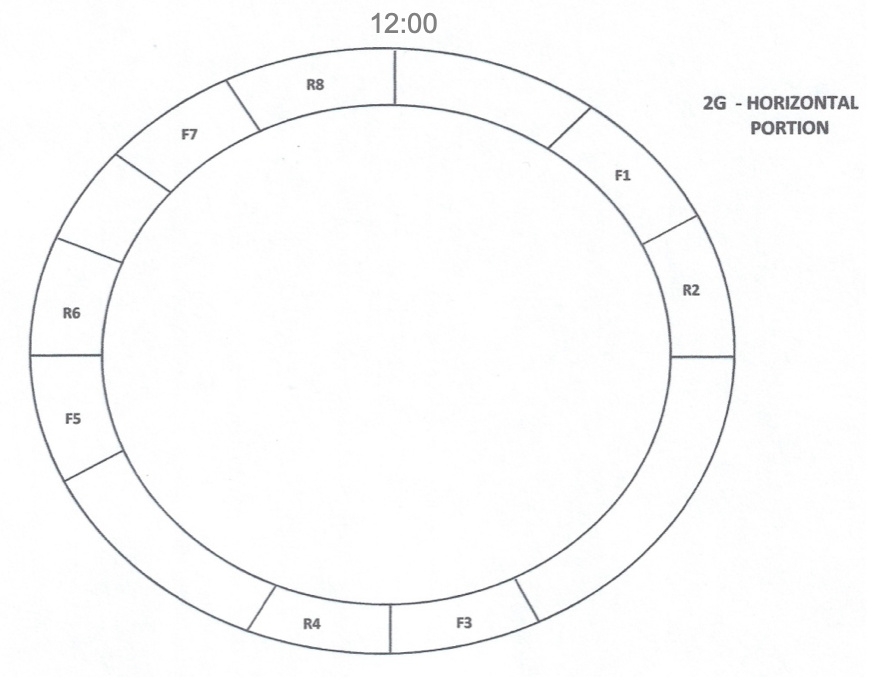
1=Face Bend (Horizontal)
2=Root Bend (Horizontal)
3=Face Bend (Overhead)
4=Root Bend (Overhead)
5=Face Bend (Vertical)
6=Root Bend (Vertical)
7=Face Bend (Flat)
8=Root Bend (Flat)
Each bend test specimen shall be die stamped by the safety officer for positive identification of the bend test specimen removal location in accordance with the above diagram. In addition, the safety officer shall stamp each bend test specimen with a “test identification number” identifying the welder who welded the test coupon and the safety officer who administered the examination.
Standards for the Evaluation of Bend Test Specimens
The guided bend tests shall have no open discontinuity in the weld or heat affected zone exceeding 1/8” measured in any direction on the convex surface of the specimen. Open discontinuities of any size are to be evaluated separately and are not cumulative. Open defects occurring on the corners of the specimen during bending shall not be considered unless there is evidence that they result from slag inclusions, lack of fusion, or other internal defects.
The failure of any bend specimen shall be considered a failure of the examination. Candidates who successfully complete the examination shall be issued a Class A Pressure Welder certificate of qualification.
Candidates Failing the Examination
A candidate who fails the examination will be issued an examination record noting the reason for failure.
A candidate failing to pass the examination for a Class A Pressure Welder certificate of qualification must wait at least 30 days before retaking the examination.
Candidates Passing the Examination
A candidate who passes the examination will be issued an examination record noting the details of the examination, including the essential variables.
The safety officer shall submit a copy of the completed examination record to Technical Safety BC who will issue a Class A Pressure Welder certificate of qualification and wallet card to the successful candidate. The Class A Pressure Welder certificate of qualification is valid for three years.
Note: The variables used and procedure followed for Class A Pressure Welder certificate of qualification examination shall not be used for pressure welding on a regulated product.
Related Information
Class A Pressure Welder
Ready to get certified as a Class A Pressure welder? Learn about the qualification requirements and exam.
Learn MoreClass R Pressure Welder
Ready to get certified as a Class R Pressure Welder? Learn about the qualification requirements and exam.
Learn MoreClass IT Pressure Welder
Ready to get certified as a Class IT Pressure welder? Learn about the qualification requirements and exam.
Learn More