Class A Syllabus Renewal
Pressure Welder Certification
Overview
This syllabus details the requirements and standards for the performance qualification test that is required for the purpose of renewing the class A pressure welder certificate of qualification.
Eligibility
A renewal applicant must hold a Class A Pressure Welder certificate of qualification issued by Technical Safety BC and must pass a performance qualification test as outlined in this syllabus.
Testing Administration
The performance qualification test shall be administered by an organization approved by Technical Safety BC as a “recognized test administrator.” The “examiner” (personnel) who administers the test shall meet the requirements outlined in the recognized test administrator’s quality control manual for certification and experience.
Application to Undertake Testing for Renewal
A candidate will need to apply at a recognized test administrator facility and pay the test fee specified by the administrator facility. The recognized test administrator will provide confirmation of the dates and times for renewal performance qualification testing.
Six months prior to the expiration date of the Class A Pressure Welder certificate of qualification, candidates are eligible to complete their performance qualification tests. If a certificate has already expired, the performance qualification must be completed within six months prior to the application.
Candidates must provide the following to the examiner prior to starting the test:
- government issued photo identification
- proof they hold a Class A Pressure Welder certificate of qualification
- welder’s logbook; and
- a copy of the Welding Procedure Specification (to be followed for the performance qualification test).
Class A Pressure Welder Certificate of Qualification Renewal Performance Qualification Test
The performance qualification test shall be conducted in accordance with this syllabus and the references made to ASME (American Society of Mechanical Engineers) Section IX; Welding, Brazing, and Fusing Qualifications.
Test Coupon
The test coupon will be sized accordingly per the Welding Procedure Specification and with consideration to the test time allowance per this syllabus. The coupon shall be welded without backing (open root) using carbon steel (P1 material) pipe, or carbon steel tube (P1 material), prepared with a bevel angle as permitted by the Welding Procedure Specification or as shown in Figure QW-469.2. The test coupon thickness will be determined by the base metal thickness range indicated by the Welding Procedure Specification and the provisions in Table QW-452.1 (b). Due to the requirement for bend testing, production welds shall not be used.
Test Positions
The test coupon shall be welded in the 6G position.
Weld Process and Procedure
Given the Welding Procedure Specification selected is in accordance with the test coupon parameters above, the candidate may follow any licensed contractor’s Welding Procedure Specification that is registered with Technical Safety BC for manual and semi-automatic processes only, with a maximum of two processes on one coupon.
The candidate will need to have a copy of the registered welding procedure specification with them for the test.
Testing Time Frame
The candidate will have two and a half (2.5) hours to prepare, tack, and weld the test coupon and one (1) hour to prepare the bend specimens.
The performance qualification test may be terminated at any stage of evaluation if the candidate fails to meet the acceptance criteria or is unable to complete the exam with the specified timeframe.
Preparation and Tacking
When preparing test coupons for tacking, the size of the root face (land) and the width of the root gap (spacing) shall be at the candidate’s discretion. Prior to tacking, mill scale, coatings, and burrs should be removed. Four tack welds, one centered at each quarter of the circumference of the pipe, are to be made using the SMAW process with an E-6010 electrode or the GTAW process using an ER70S-2 filler metal and should be approximately ½” to ¾” in length before feathering. All tack welds are to be considered part of the weld and should be of acceptable quality with no cracks, complete fusion, and joint penetration.
Welding
After the candidate completes tacking the coupon, they will present it to the examiner for evaluation.
If the examiner has accepted the coupon, it will be positioned for welding in the 6G position. The examiner will mark the position and height of the coupon. Once the coupon is positioned for welding, the marked coupon and positioner shall not be moved. The candidate will then weld the root pass, using the appropriate filler metal. When the candidate completes the root pass, the coupon shall remain in position and the weld shall be evaluated by the examiner. An acceptable root pass shall show no cracks, complete joint penetration, and complete fusion of the weld and base metals. In addition, the root pass should also be of uniform width, the penetration at least flush with a maximum reinforcement not exceeding 1/8 of an inch, and free of undercut or porosity.
If the root pass is acceptable to the examiner, the candidate shall complete the hot pass, fill, and cap passes. Upon completion of the hot pass, fill and cap passes, the coupon shall remain in position and the weld shall be evaluated by the examiner. The cap shall be completed using the technique as described in the Welding Procedure Specification, which shall show no cracks, complete joint penetration, and complete fusion of the weld and base metals. The cap should also be of uniform width, filled at least flush with a maximum reinforcement not exceeding 1/8 of an inch, and free of any undercut, porosity, or arc strikes.
Bend Testing Specimens
The guided-bend test specimens shall be either transverse side or transverse face and root bends; prepared based on the size and thickness of the pipe or tube test coupon in accordance with the provisions of American Society of Mechanical Engineers (ASME) Section IX. The jig and bend radius shall be in accordance with figures QW-466.1, QW466.2, and QW-466.3.
Conforming to the provisions of QW-462.2 or QW-462.3(a), the test specimens shall have weld reinforcement ground flush on both sides with edges deburred. Candidates may SYL-BP-107 Rev. 1 (2022-06-28) Page 5 of 6 radius the corners of the specimens to a maximum of 1/8 of an inch. Excessive grinding that reduces the thickness of the specimens (on either side) below the nominal thickness shall result in a failed test.
Each bend test specimen shall be removed in accordance with figure QW-463.2(d) or Figure QW-463.2(e). Each bend test specimen to be removed shall first be die stamped by the examiner for positive identification. At the top end of the coupon, each bend test specimen shall be stamped with the test identification number. On the lower section, each bend test specimen shall be stamped with the location of removal, moving in a clockwise direction starting from the 12:00 position.
Standards for the Evaluation of Bend Test Specimens
The guided bend tests shall have no open discontinuity in the weld or heat affected zone exceeding 1/8 of an inch measured in any direction on the convex surface of the specimen. Open defects occurring on the corners of the specimen during bending shall not be consideredunless there is evidence that they result from slag inclusions, lack of fusion, or other internal defects.
A failed bend test specimen shall be considered a complete failure of the test.
Failing the Performance Qualification Test
A candidate failing to pass a renewal performance qualification test may arrange with the recognized test administrator to take an immediate retest in accordance with the recognized test administrator’s quality control program, QW-321.1 and QW-321.2 of ASME Section IX.
Passing the Performance Qualification Test
The examiner shall be responsible for recording and certifying the test results on a QW484A form, for a candidate who passes their welder performance qualification test.
The examiner will issue the successful candidate a completed and certified (by signature) QW-484A performance qualification record. This document will include details of the welding procedure specification identification, welding process, materials, filler metals, weld metal thickness, diameters, and positions/progressions in which the candidate has demonstrated their qualification.
The examiner will record the successful performance qualification test variables on one line, and the class A renewal record on the second line in the Technical Safety BC section of the candidate’s logbook. The entry shall include the examiner’s name, signature, certification body registration number (CWB or ABSA Welding Examiner SYL-BP-107 Rev. 1 (2022-06-28) Page 6 of 6 Number),and “TP” number of the recognized test administrator organization.
Sample logbook entry:
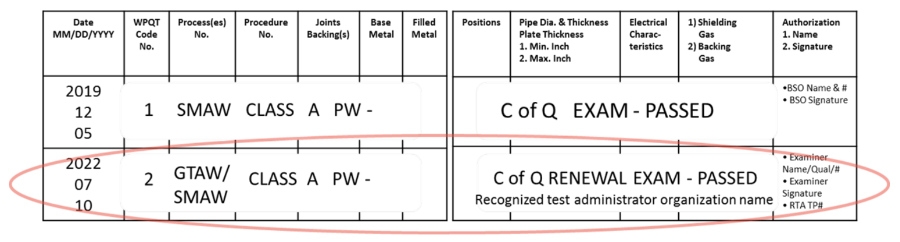
Candidate's Responsibilities
A Class A Pressure Welder certificate of qualification is valid for three years. The expiry date shall appear on the certification approval notice, wall certificate, and wallet card. The candidate must renew their certificate of qualification before its expiry date if they wish to continue to perform regulated work in province of British Columbia. If a certificate has already expired, the performance qualification test must be completed within six months prior to application.
The candidate shall be responsible for completing the Class A renewal application via their Technical Safety BC online services account. This renewal application will involve submitting a copy of the certified QW-484A record, picture(s) or scan(s) of the entry into the Technical Safety BC Section of the welder’s logbook and paying a specified renewal fee.
NOTE: A current Class A Pressure Welder certificate of qualification must be available at the site where pressure welding is being performed, in addition to the welder’s logbook with the applicable performance qualification test(s) entered for the pressure welding being performed. The continuity section of the welder’s logbook must be current and in accordance with the requirements of ASME Section IX for the applicable welding process.
Related Information
Class A Pressure Welder
Ready to get certified as a Class A Pressure welder? Learn about the qualification requirements and exam.
Learn MoreClass R Pressure Welder
Ready to get certified as a Class R Pressure Welder? Learn about the qualification requirements and exam.
Learn MoreClass IT Pressure Welder
Ready to get certified as a Class IT Pressure welder? Learn about the qualification requirements and exam.
Learn More